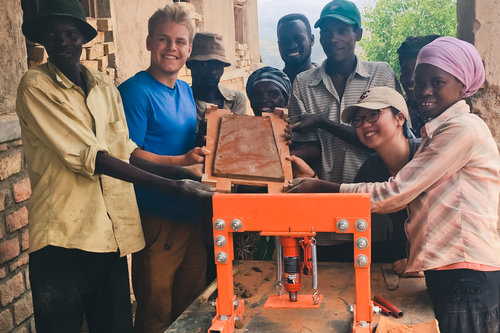
Overview
The overall goal of the tile press is to compact the clay and remove air bubbles, ultimately creating stronger, higher quality roof tiles. The hydraulic tile press was designed and implemented by EWB-SCU in 2017, replacing a purely mechanical tile press implemented in 2015. Without a press, the community scrapes the top of clay in a roof tile mold. Because the clay is not compacted, air bubbles remain in the clay weakening the integrity of the tile. By increasing the quality of the CO-OP’s tiles, the community could sell their tiles for more money, increasing their income without spending resources.
Background
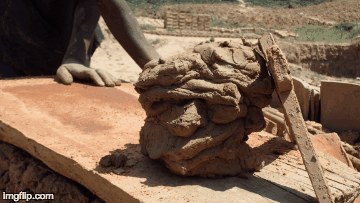
In 2015, EWB-SCU attempted to improve the pressing process as their first project. The original team had not visited the community before and struggled to understand the tile making process, lacking critical details such as the density and thickness of the clay. They did their best with the limited information they had to address the clay press problem and traveled for the first time bringing a table, an arbor press, and tile molds to the community.
In 2016, EWB-SCU returned to the community and saw that the tile press was too weak to sufficiently compress the clay and did not distribute load evenly across the tile. Additionally, it was prone to dirt getting in the mechanical components, adding friction and making the system more difficult to use. As a part of EWB-SCU’s long term commitment to the community, the team realized that the press would need to be redesigned.
Design: Hydraulic Jack
EWB-SCU returned in 2017 with an improved press that could mediate the deflection of the table and apply up to 4,000 lbs, more than 15x the force of the arbor press.
To create the press, the team started by brainstorming ways to press the clay. They ultimately decided to use a hydraulic jack because of its small profile and ability to produce massive force. To contain this force, a custom frame needed to be designed. Steel was chosen due it its high strength, and standard cross sections (1x1 in & 1x2 in) were used to cut costs. Standard off the shelf Unistrut brackets were chosen to connect the steel tubing because of their strength. The frame and brackets were analyzed using finite element analysis (FEA) and hand calculations for bending and bearing stresses. Taking into account the strength of the frame, a 2 ton hydraulic jack was selected because it would have enough strength compress the clay and would leave a margin of safety to ensure that the frame would not bend or suffer from fatigue.
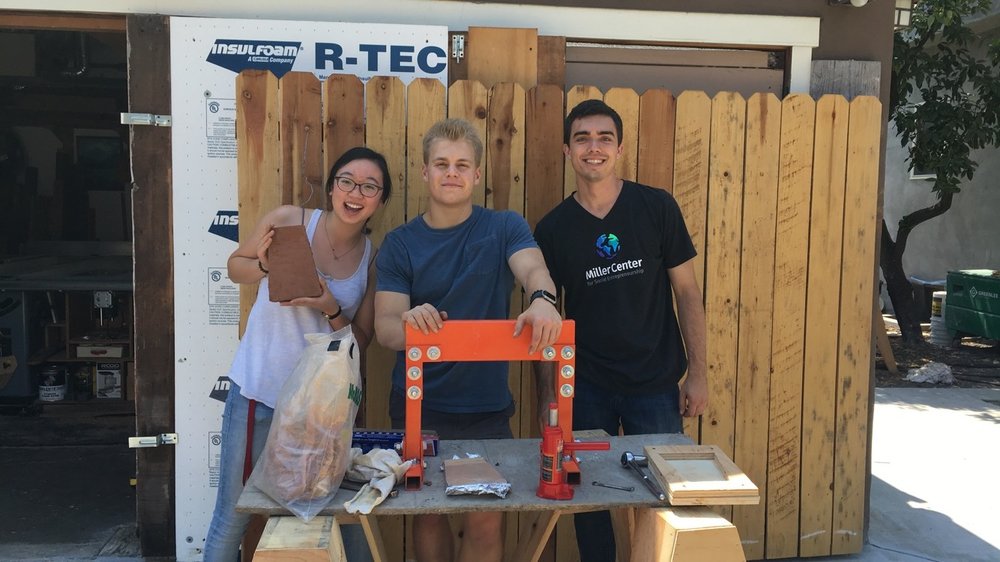